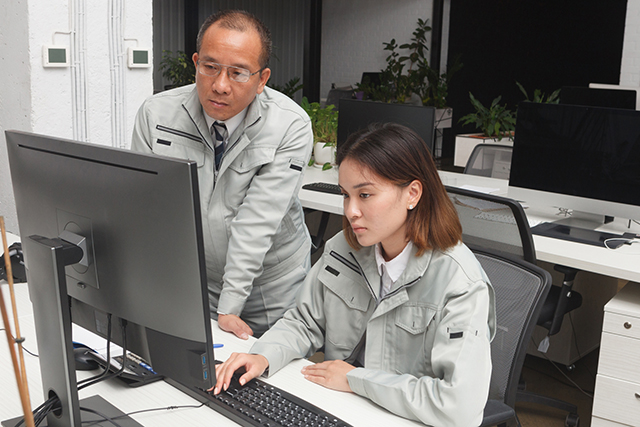
これまでの事後保全、予防保全といった設備保全とは異なる新しい保全方法として注目されているのが「予知保全」です。予知保全はほかの保全方法とは何が違うのか、その概要やメリットについてご紹介します。
予知保全とは
予知保全とは、工場や生産現場の機械・設備を継続的に安定稼働させるために、機械・設備の状態を連続的に計測することでいち早く劣化や不具合を検知もしくは予測して、故障に至る前に修理や部品交換を行う保全方法です。
ポイントは、予知保全においては機械・設備の状態を常に監視し続けるという点にあります。その監視によって何らかの変化をリアルタイムで捉え、故障や不具合の予兆を見つけ出すわけです。そのため予知保全を行うには、常に機械・設備を監視し続けるシステムが必須です。
現在、その監視システムにはIoTやAI技術が多く使用されています。各種センサを備えたIoTデバイスが機械・設備の状態をモニタリングし、その時系列データをAIが分析して異常が起きつつあると判断するとアラームを発する、というのが大まかな仕組みです。
IoTデバイスがモニタリングする対象にはさまざまなケースがありますが、代表的なものとしては製造装置のモータの「軸受」という部品が挙げられます。軸受に振動センサを取り付け、振動の波形、周波数、振幅の状態などを監視してネットワークを介してクラウドなどに送信するというのが典型的な方法です。
一方、AIによる予知保全には機械学習やディープラーニングのようなアルゴリズムを用いるのが一般的です。どのようなアルゴリズムを選択するべきかは対象となる機械・設備と時系列データの量・内容によって変わります。このようなアルゴリズムには「教師データあり学習型」「教師データなし学習型」「強化学習型」がありますが、これも大まかにいうなら、データの特徴を人が捉えられているのであれば教師データを作成できるということですから「教師データあり学習型」を、データが膨大すぎるなど特徴そのものもAIが学習する必要があるなら「教師データなし学習型」が適しています。
ちなみに「強化学習型」は、囲碁・将棋・チェスなどで名人と対戦するような、目的に向かって膨大な試行錯誤を行うアルゴリズムとなっています。
予知保全とほかの保全方法との違い
予知保全と似た言葉に、予防保全と事後保全があります。それぞれの意味は以下のとおりです。
予防保全
機械・設備を安定稼働させるために、部品ごとの耐用時間を定めておき、定期的に交換する保全方法です。この場合の部品交換は、実際に劣化や不具合が見られない場合でも実施されます。ただし、一定期間で必ず交換する「時間基準保全」のほかに、部品の劣化具合を確認してそれに応じて交換する「状態基準保全」という方法もあります。
予防保全のメリットは、定期的なメンテナンスによって故障するリスクを最小限に抑えられると同時に、計画的な作業によって機械・設備の停止をメンテナンス時だけに限定できることです。
事後保全
機械・設備が故障したときや機能低下が見られたとき、あるいは不良品が発生したときなど、何か問題が起きたあとに部品交換や修理などの対処をする保全方法です。設備保全の方法としては最も古くから行われていたものの一つです。問題が起きたときに、いかに素早く原因を突き止め、修理をするかがポイントになります。
事後保全のメリットは保全費用を最小限に抑えられることです。ただし、計画外の機械・設備の停止時間=ダウンタイムの発生に伴う損失は避けられません。
予知保全のメリット
予知保全は、事後保全や予防保全よりも新しい保全方法です。故障の予兆を100%確実に捉えられるのであれば、予知保全ではほかにはない多くのメリットを得られます。
事後保全では修理のためのダウンタイムが発生します。予防保全を行っていても定期的な機械・設備の停止はすることになり、突然の故障による計画外のダウンタイムが生じる確率もゼロではありません。しかし予知保全が完全に機能すればダウンタイムを最小限に抑えられます。ダウンタイムの回避または短縮は、工場の生産性の向上をもたらします。
交換部品の在庫を減らし、部品交換費用を抑えられるのもメリットです。事後保全や予防保全では故障が起きたときに備えて余裕を持った交換部品を確保しておく必要があります。しかし、予知保全では機械・設備の状態に応じて部品の発注や補充を行うことが可能です。また、予知保全は機械・設備のモニタリングは保全システムにある程度任せることができ、アラートが発せられたときだけ部本交換のために人員を動かせばよいことになります。そのため保全のための人件費も削減できます。
予知保全を始めるために必要なこと
予知保全を始めるには、IoTによる機械・設備の監視と、AIによる時系列データ分析という2つをそろえる必要があります。
そのためにはまず、IoT技術によって何をどのくらいの頻度でセンシングすれば予知保全のための最適なデータが得られるのかを確定させなければなりません。また、的確なデータを得るための環境を整えられたら、そのデータをAIが分析して故障の予兆を確実に捉えられるようにするためのアルゴリズムの選定や、学習期間も必要です。
現在、予知保全のためのソリューションがいくつかのベンダーから提供されています。また、工場内設備の監視と分析を容易に実現するための予知保全プラットフォームなども登場しています。自社の要件に適したサービスを選定できれば、予知保全システムを有効に導入・運用することが可能でしょう。
「壊れる前に直す」という画期的な保全方法である予知保全は、ダウンタイムの発生を抑制し、工場や生産現場の生産性を最大限に向上させる可能性を持っています。近年、身近なものになってきた予知保全の導入を検討してみてはいかがでしょうか。